Originally Posted By: JiL
Clinebarger, thank-you for sharing such good tech info! I'm on the fence with dual feeding a 4L80 in a pickup and have a few question if I may:
Originally Posted By: clinebarger
The slower reverse apply is my biggest concern, Just be patient & let it latch up before applying throttle.
What's the ball-park for how much slower? Are we talking a partial second, or could it be two or three seconds? Does leaving out the Reverse check ball help with this?
Originally Posted By: clinebarger
During full throttle 3-1 & 3-2 automatic/forced downshifts, The direct piston return springs are not strong enough to return the piston in a timely manner because it's trying evacuate 200% more ATF than the circuit was designed to evacuate, Over time this WILL distress the direct frictions.
I HIGHLY recommend "High Rate" return springs in any dual feed hydramatic transmission.
Do the stiffer springs FIX the issue or just reduce the release drag to a semi-tolerable level? I saw elsewhere (from you?) that removing the seal lands, in addition to the seal, from the center support can help speed release?
Originally Posted By: clinebarger
Dual Feeding the directs is a fantastic modification.......On rigs making north of 450 horsepower!! I rarely do this mod on a heavy duty unit, It is just not warranted.
Below that currently at about 385, but the future could add some to that. . .
My apologies to joegreen if I'm sidetracking too much!
1st question. Reverse "Latch-up" time varies by what Pressure Regulator Spring, Boost Valve, & Orifice sizes in the Separator Plate are used, The delay is small in most cases(10th's of a second over what it was). But on a plow truck, Work trucks that back trailers often, A truck that gets stuck in the mud/ice often, Or just an impatient driver CAN damage/distress the Direct frictions......Because these operators never cared in the first place how long it took, The only reason I made that statement was because I thought Joe's truck was dedicated to plowing.
YES, Removing the #9 checkball will dramatically reduce latch-up times, At the same time Reverse will become VERY harsh.....Not good on the drive splines on the Direct frictions, Direct Drum to Sun-Gear shaft splines, U-joints & Really bad on the Transfer Case if equipped.
If you want to do a modification to quicken the circuit apply.....Increase the size of the orifice feeding Direct clutches in reverse (Red Circle) by 20%.
2nd question. The springs help many high rpm issues with the Direct Clutch, Quicker release & prevents "Centrifugal Piston Creep" in lower gears.
Face Grooved frictions also help with friction to steel separation & Oiling of the friction faces when the frictions are overrunning.
I remove the center lip seal in the Drum & Omit the second sealing ring on the center support on every dual feed TH400/4L80E. Machining the unused ring lands off the Center Support increases flow rates during apply & release.
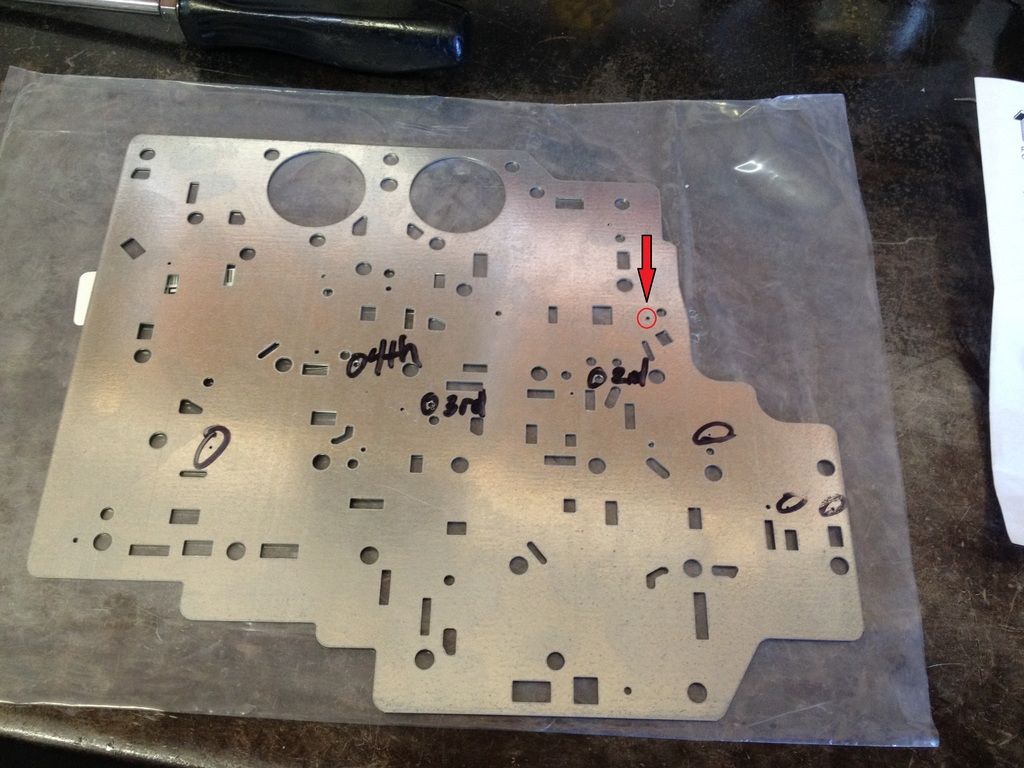