From time to time i see people asking about oil filter cutters. Here is one i made for about $20. The cutting blade was the biggest one farm and fleet had. They have 3 sizes to choose from. The bearings i think came from a roller skate. The vice was from harbor freight.
The cutter wheel hole was not big enough for a shoulder bolt so i used a bridge design to hold the cutter in place.
I had to extend one of the jaws with a piece of wood so the oil filters had someplace to sit. This design will cut two different size oil filters, The smaller type for smaller car engines and lawn tractors and the next size up for bigger engines.
The important thing is to have both sizes of oil filter on hand so you can check spacings and adjust the height of the cutter and bearings as you are building it.
Adjust the height of bearings were they track the best.
If you have a drill press this will be very easy to build, the holes will all be square and easy to drill. The vice is cast iron and drills and taps very easily.
This is a very forgiving design and can incorporate a lot of whatever you can scrounge up.
As built.
Cutter blade dia. .8"
Center of cutter blade to vise surface .4” MIN height.
Spacing of bearings 3.125”
Bearing dia approx .8”. I had bearings from American Science and Surplus that were inch size. The center hole was ¼ inch. The closest common bearing is a 8mmx22mmx7mm roller skate bearing.
Wood extension of jaw 1 1/8"
4 inch drill press vice Harbor Freight, looks like prices went up a little. I paid $12 now it is $17.
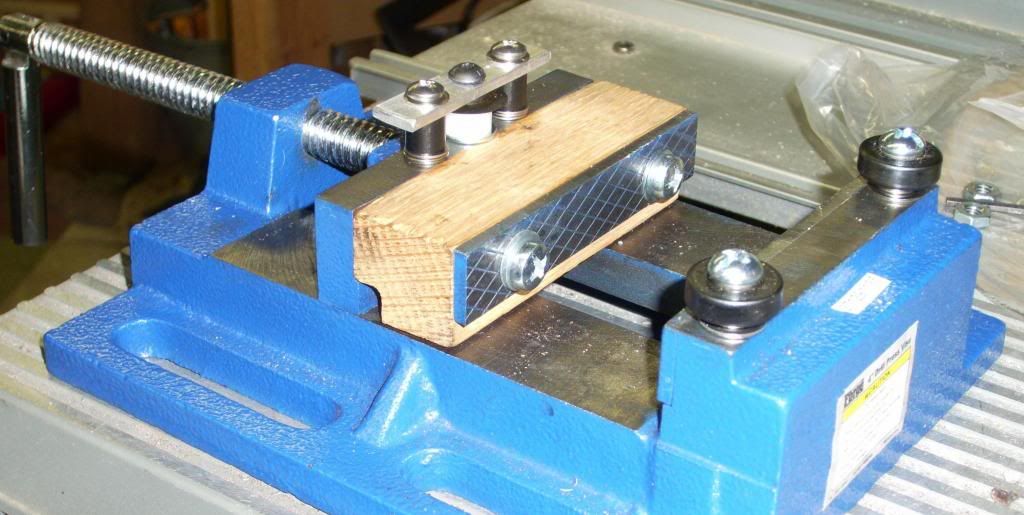
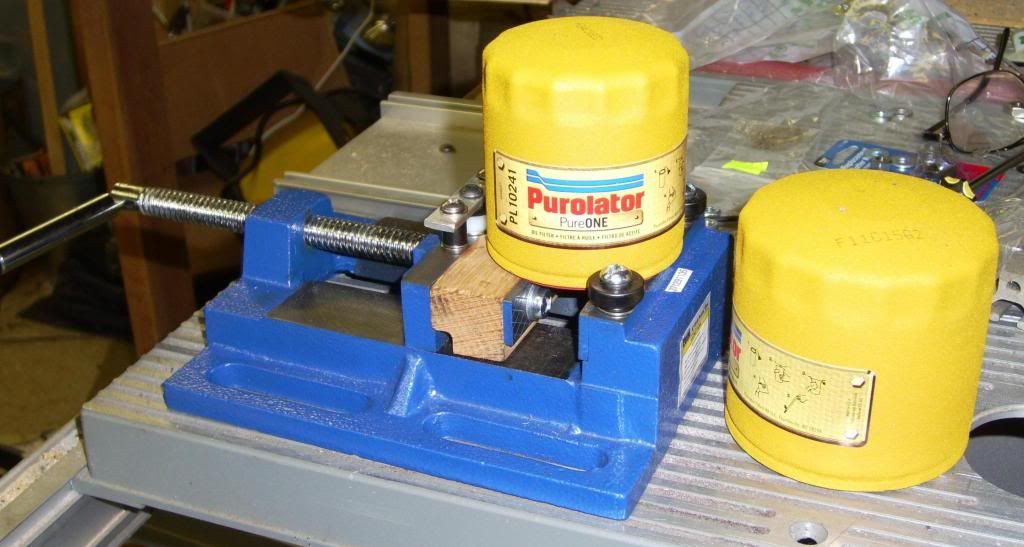
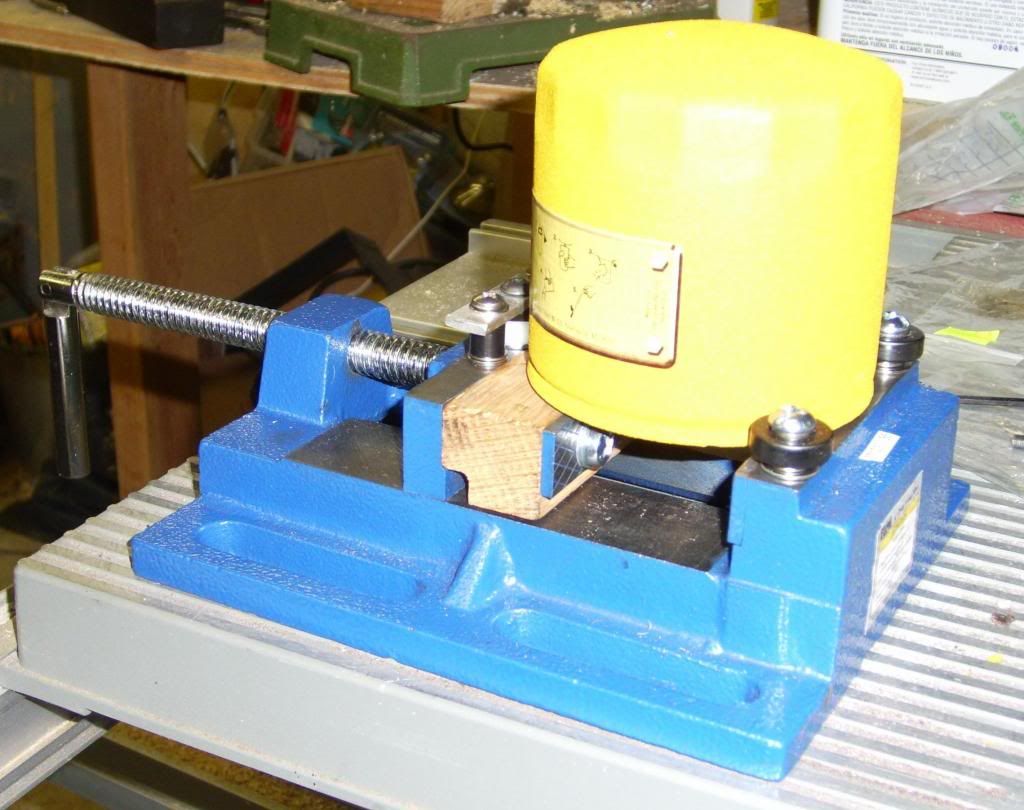
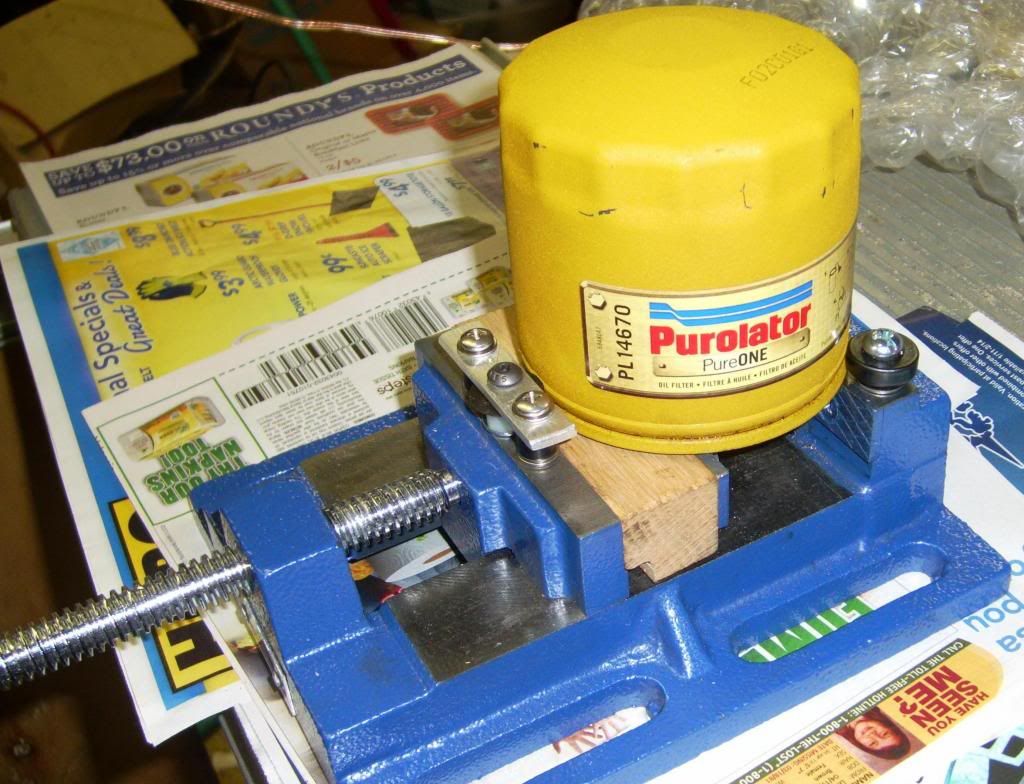
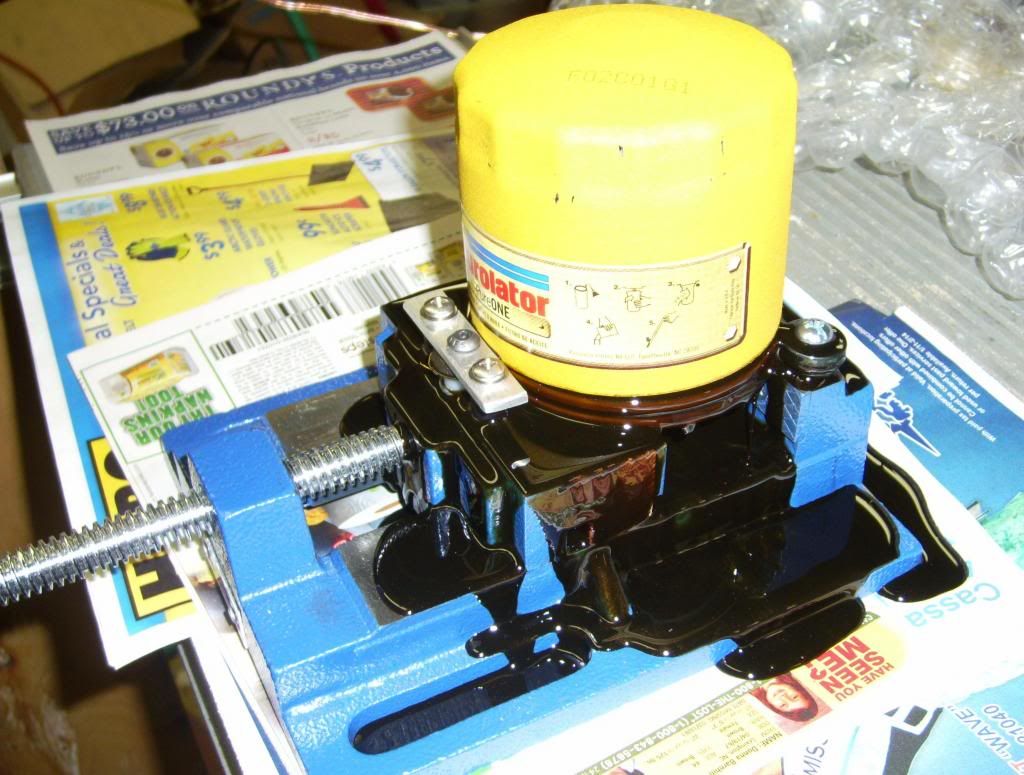
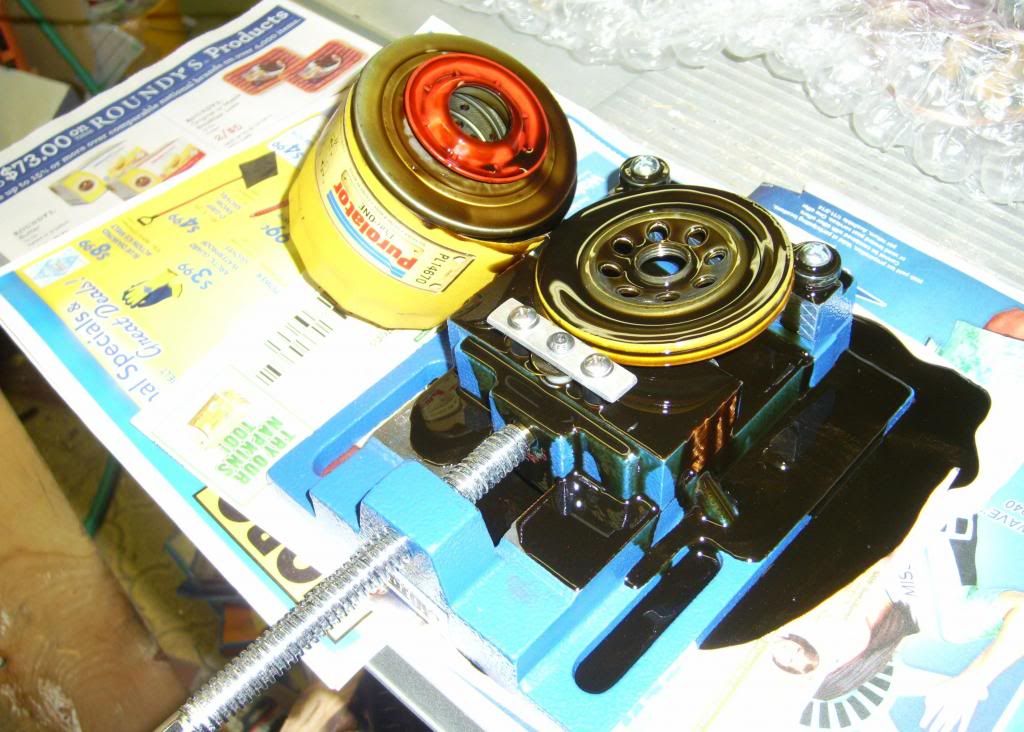
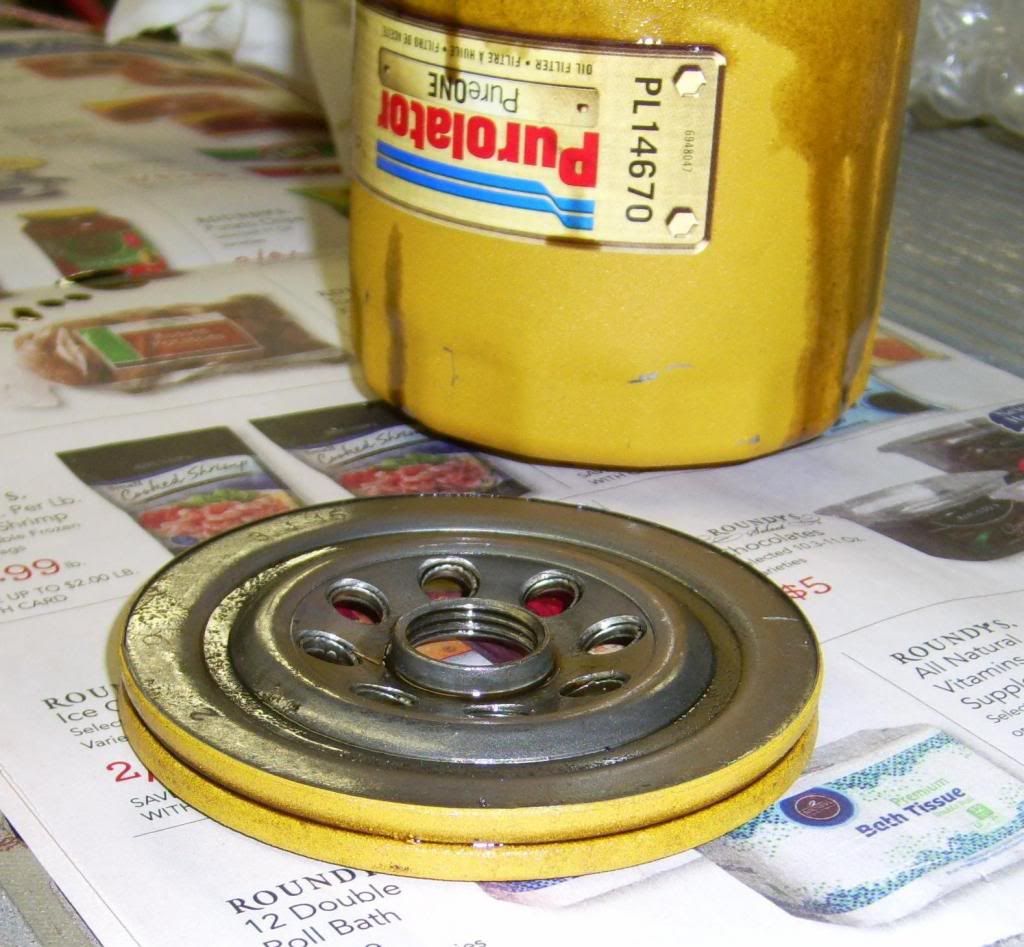
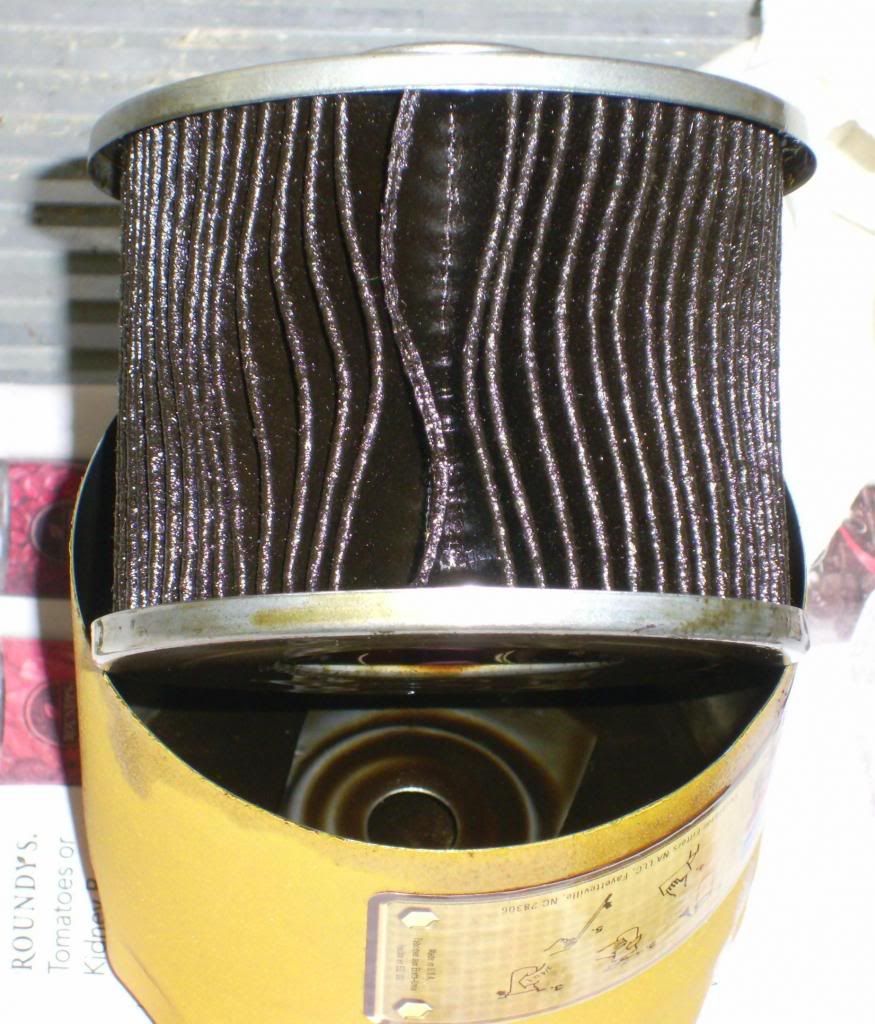
The cutter wheel hole was not big enough for a shoulder bolt so i used a bridge design to hold the cutter in place.
I had to extend one of the jaws with a piece of wood so the oil filters had someplace to sit. This design will cut two different size oil filters, The smaller type for smaller car engines and lawn tractors and the next size up for bigger engines.
The important thing is to have both sizes of oil filter on hand so you can check spacings and adjust the height of the cutter and bearings as you are building it.
Adjust the height of bearings were they track the best.
If you have a drill press this will be very easy to build, the holes will all be square and easy to drill. The vice is cast iron and drills and taps very easily.
This is a very forgiving design and can incorporate a lot of whatever you can scrounge up.
As built.
Cutter blade dia. .8"
Center of cutter blade to vise surface .4” MIN height.
Spacing of bearings 3.125”
Bearing dia approx .8”. I had bearings from American Science and Surplus that were inch size. The center hole was ¼ inch. The closest common bearing is a 8mmx22mmx7mm roller skate bearing.
Wood extension of jaw 1 1/8"
4 inch drill press vice Harbor Freight, looks like prices went up a little. I paid $12 now it is $17.
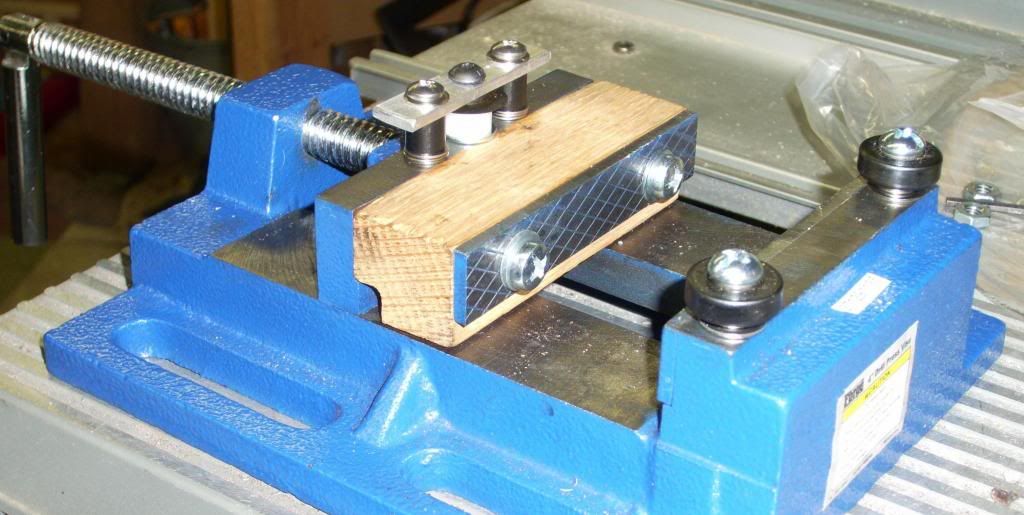
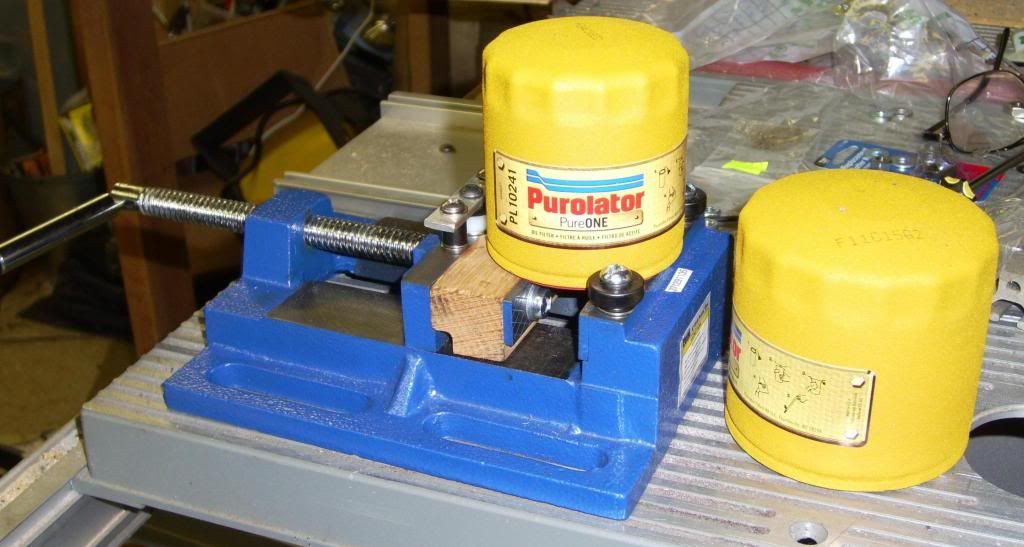
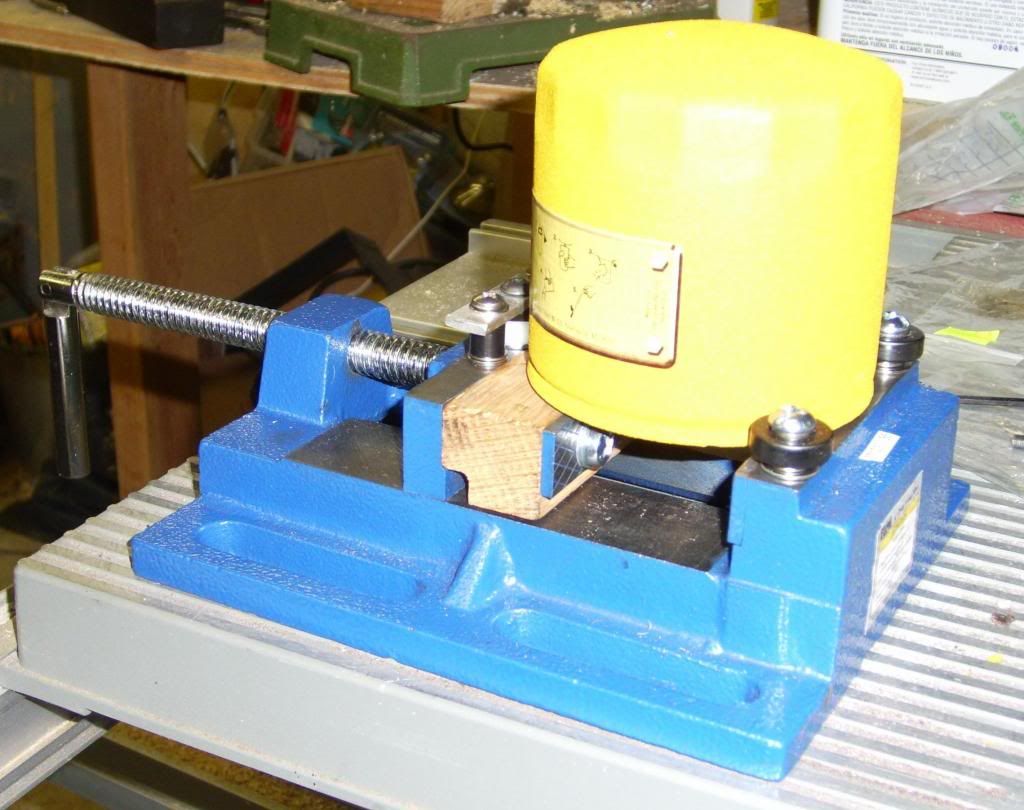
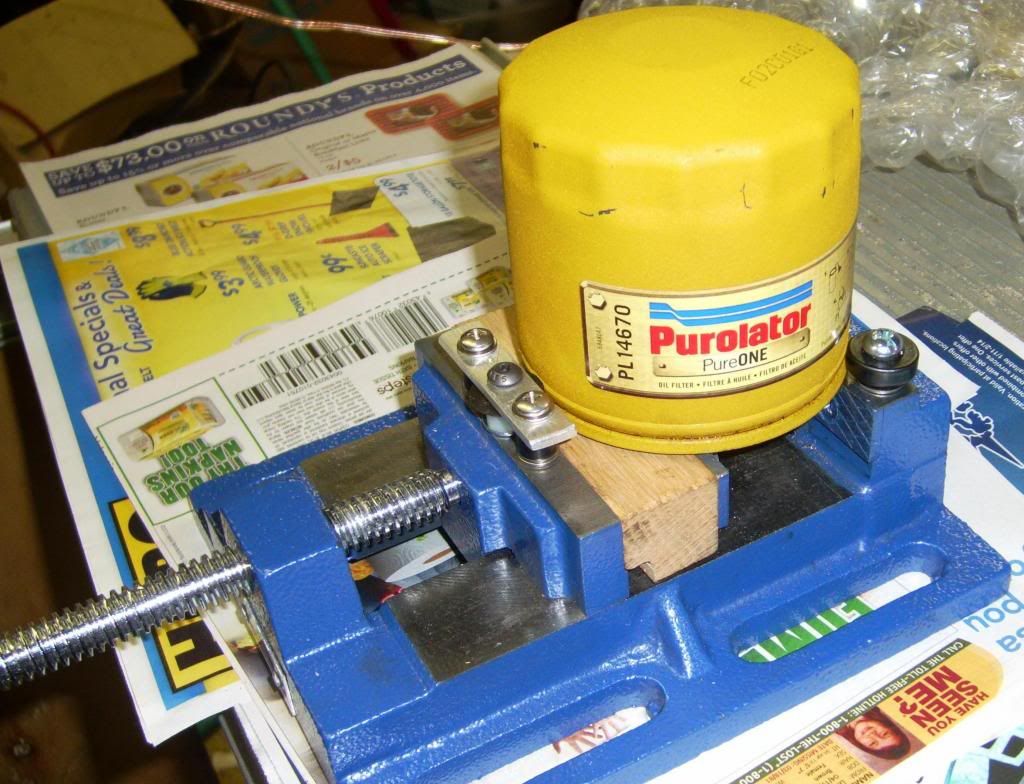
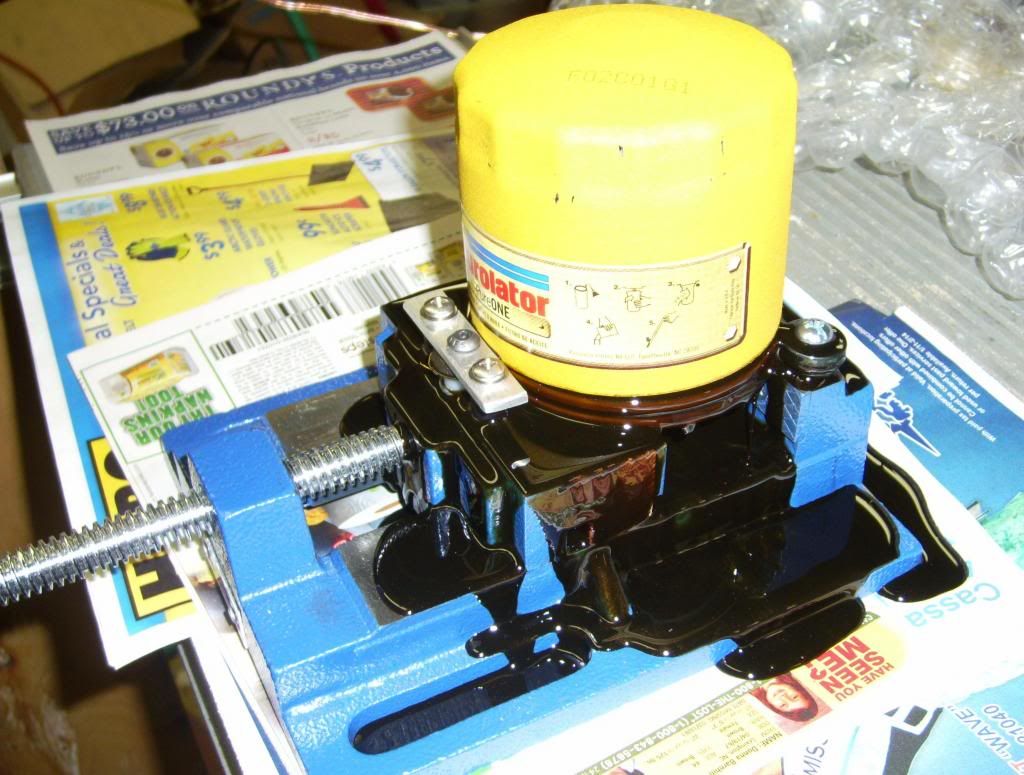
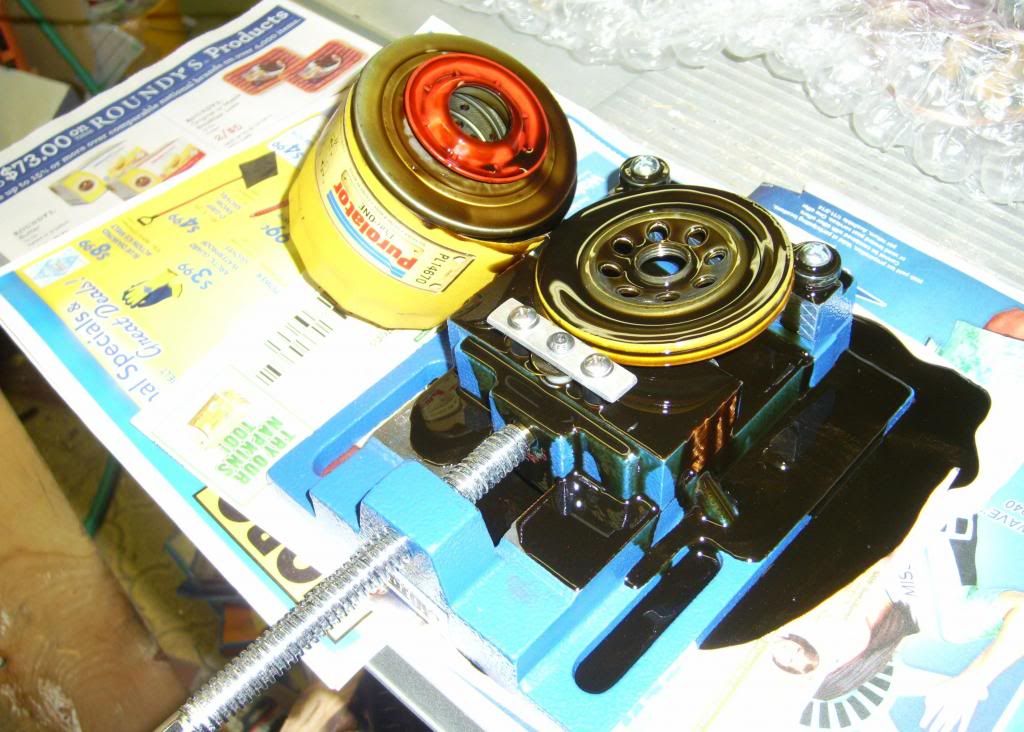
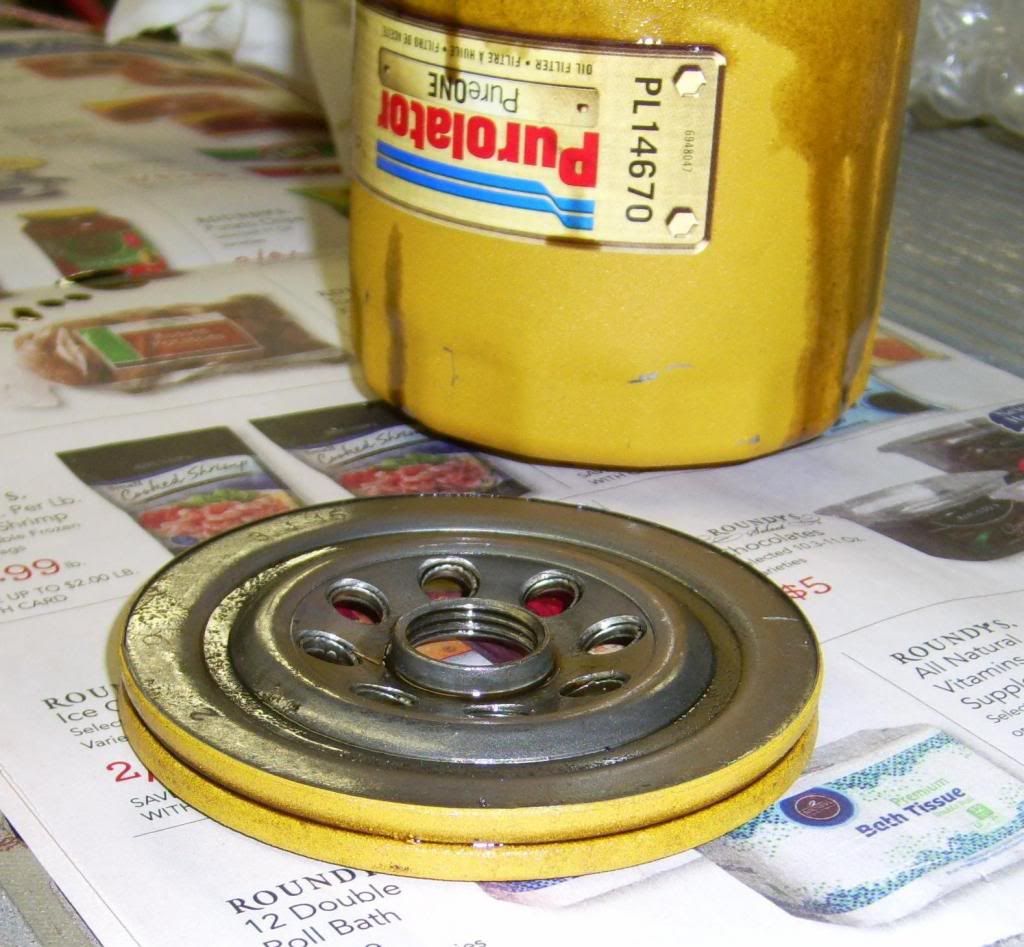
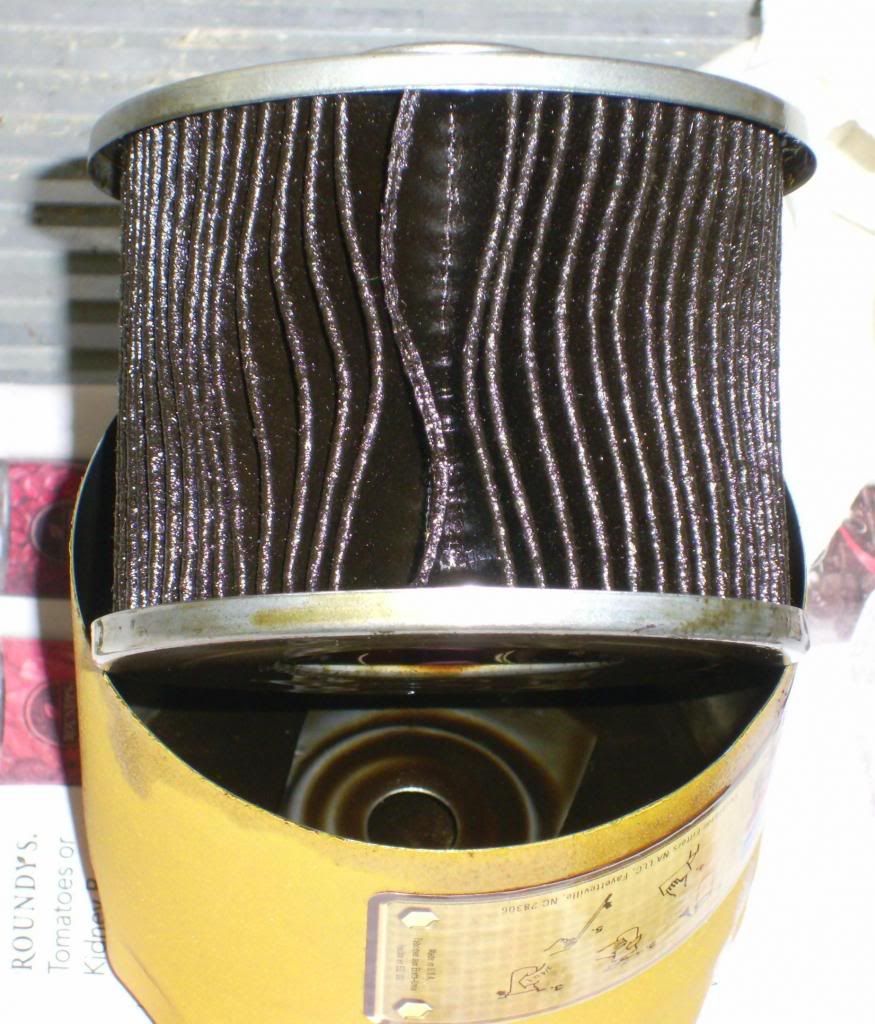
Last edited: